- HOME
- NEWS
- Working in Pure Titanium and Titanium Alloy material
Working in Pure Titanium and Titanium Alloy material
2019.08.07
The Medical industry and Aerospace industry mould almost use of Pure Titanium and Titanium Alloy material.
Those materials of property belong to difficult material. The chips adhered to knife-edge easily and remove chips is very difficult
when cutting those materials. It is not good for tool life and easy break. (ex. Fig. 1)

.jpg)
<Fig. 1> The chips adhered to knife –edge in tool
DHF owns a superior R&D term, as well as an application center, providing persistent tooling tests, developing innovative products and found best coating.
Of course, this process is quite hard, but also overcome, titanium good cut products finally listed in 2009,
We provided all procedures to customers with reference. The details are as following.
a: When the tool has improper groove design, it was unable to break chip, and make long extrusion-like chip easy. (ex. Fig. 2)
b: When the tool has best geometry to design, the chip is a sheet. The meaning is tool has good life and best cutting power.(ex. Fig. 3)
.png)
<Fig. 2> Imperfect chips shape <Fig. 3> Perfect chips shape
The traditional VC of milling Titanium only reaches 40-60m/min, DHF breaks the old concept, increases the working performance, and extends tool’s life. Through our R&D testing, our Titanium series could have Vc up to 100-150m/min; if in the conditions of good chip removal, it can do 0.8D machining of Aa and Ap. DHF Titanium Series has completed size, and also have different designs and selections for slotting, side milling surfacing and thread milling.
The following description is about DHF Titanium Series products:
A. UTW
1: Special waves design; the Vc can do 12-150m/min.
2: High Speed, High Feed and large Depth of cutting; it is good at Roughting.
3: It can do a 0.5D to 0.8D machining for both Slotting (Aa) and Side milling.
B. UTH / UTHR
1: UTH/UTHR is good at Roughing and Finishing.
2: Special high helix design; the Vc can do 130m/min.
3: It can do a 0.5D to 0.8D machining for both Slotting (Aa) and Side milling.
4:Finishing enables the optimum surface.
C. UTJ
1: UTJ is good at Roughing and Finishing.
2: Special grooving concept and design features smooth chip removal and low stickiness.
3: UTJ is good for side milling and depth of cutting is 3D milling.
D. WWB
1: WWB is good at Roughing.
2: It is good for pure Titanium and Titanium blank cutting<ex. Fig. 4>
3: It can do a 0.5D to 0.8D machining for both Slotting (Aa) and Side milling.
We must understand the characteristics and cautions, when you would like to cutting Titanium series of material. We shared our experience as following.
Characteristics of titanium: alloy: the density is less 4.5g/cm3, only 60% of the iron, usually known it with aluminum, magnesium as a light metal and opposite titanium alloy, aluminum alloy and magnesium alloy called light alloy.
Many countries know the importance of titanium materials and they are research, development and application of the titanium material.
Titanium in the 1950s is an important structural metal. It has high strength, good corrosion resistance, high heat resistance and easy welding characteristics, used in various fields, especially high strength, easy welding performance is conducive to the manufacture of golf club head.
In 1954, USA succeeded in developed Ti (titanium)-6Al (aluminum)-4V (alum) alloys.
Ti-6Al-4V alloy have heat resistance, strength, ductility, toughness, formability, weldability, corrosion resistance and biocompatibility aspects to achieve better standards. The people use of Ti-6Al-4V alloy arrived for 75 to 85% of all titanium alloys.
When the hardness of titanium is greater than the HB350, the cutting will be particularly difficult. When the hardness of the titanium alloy is less than the HB300 is prone to stick the knife phenomenon is not easy to cut.
Titanium alloy, the chemical affinity of the tool material, cutting power under the conditions of the high cutting temperature and per unit area, the tool is very prone to adhesive wear, such as the <ex. Fig. 1>.
Titanium thermal conductivity is very small (equivalent to S45C 1/5 ~ 1/7),
The chip and rake face contact length is very short, the heat is not easy to release when the cutting. The heat is mainly concentrated in the smaller scale of the cutting area and near the cutting edge. The cutting temperature is high.
Chemical activity of titanium in the high cutting temperature, the external can easily absorb the oxygen and nitrogen in the air. They changed their characteristic easily. (ex. Hard and brittle) At the same time of plastic deformation in the cutting process can also cause surface hardening.
Chilled phenomenon will not only reduce the fatigue strength of parts and easy damage tool. So it is a very important feature when cutting titanium.
Titanium Alloy blank pass through many process. It changes into hard, brittle and uneven in surface. The flutes damage caused this condition. ( We recommend Titanium series of WWB. WWB can easy to solute this difficult problem.) (ex. Fig. 4)
.jpg)
<Fig. 4>Titanium Alloy blank
The collection of points as above, please note the following important points when you produce Titanium and Titanium Alloy.
A. Select the appropriate tool.
B. Use high-pressure emulsion machining (ex. Fig. 5)
C. Correct cutting data.
D. Programs (CAM) is also very important.
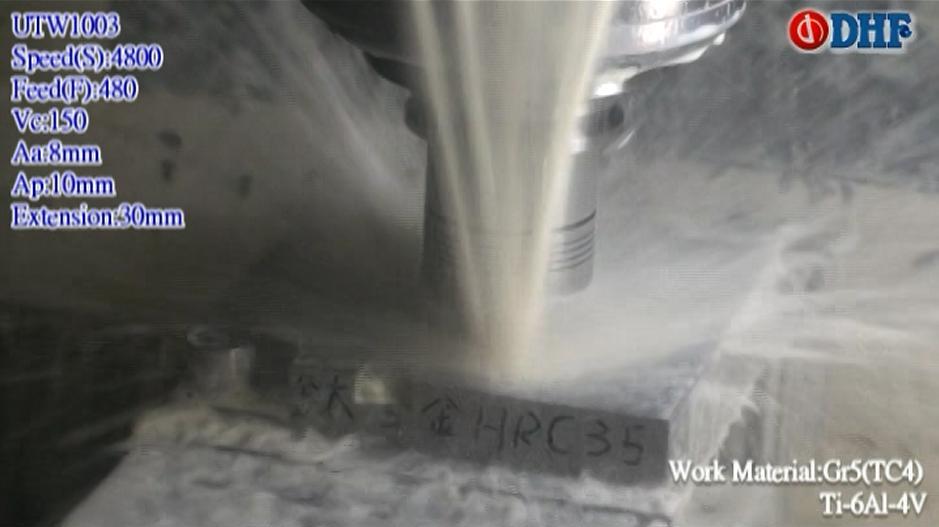
<Fig. 5> Example for use high-pressure emulsion machining
Understand the product feature and the right choice in order to show the excellent tooling capacity.
Written by DHF Technology Center
Those materials of property belong to difficult material. The chips adhered to knife-edge easily and remove chips is very difficult
when cutting those materials. It is not good for tool life and easy break. (ex. Fig. 1)

.jpg)
<Fig. 1> The chips adhered to knife –edge in tool
DHF owns a superior R&D term, as well as an application center, providing persistent tooling tests, developing innovative products and found best coating.
Of course, this process is quite hard, but also overcome, titanium good cut products finally listed in 2009,
We provided all procedures to customers with reference. The details are as following.
a: When the tool has improper groove design, it was unable to break chip, and make long extrusion-like chip easy. (ex. Fig. 2)
b: When the tool has best geometry to design, the chip is a sheet. The meaning is tool has good life and best cutting power.(ex. Fig. 3)
.png)
<Fig. 2> Imperfect chips shape <Fig. 3> Perfect chips shape
The traditional VC of milling Titanium only reaches 40-60m/min, DHF breaks the old concept, increases the working performance, and extends tool’s life. Through our R&D testing, our Titanium series could have Vc up to 100-150m/min; if in the conditions of good chip removal, it can do 0.8D machining of Aa and Ap. DHF Titanium Series has completed size, and also have different designs and selections for slotting, side milling surfacing and thread milling.
The following description is about DHF Titanium Series products:
A. UTW
1: Special waves design; the Vc can do 12-150m/min.
2: High Speed, High Feed and large Depth of cutting; it is good at Roughting.
3: It can do a 0.5D to 0.8D machining for both Slotting (Aa) and Side milling.
B. UTH / UTHR
1: UTH/UTHR is good at Roughing and Finishing.
2: Special high helix design; the Vc can do 130m/min.
3: It can do a 0.5D to 0.8D machining for both Slotting (Aa) and Side milling.
4:Finishing enables the optimum surface.
C. UTJ
1: UTJ is good at Roughing and Finishing.
2: Special grooving concept and design features smooth chip removal and low stickiness.
3: UTJ is good for side milling and depth of cutting is 3D milling.
D. WWB
1: WWB is good at Roughing.
2: It is good for pure Titanium and Titanium blank cutting<ex. Fig. 4>
3: It can do a 0.5D to 0.8D machining for both Slotting (Aa) and Side milling.
We must understand the characteristics and cautions, when you would like to cutting Titanium series of material. We shared our experience as following.
Characteristics of titanium: alloy: the density is less 4.5g/cm3, only 60% of the iron, usually known it with aluminum, magnesium as a light metal and opposite titanium alloy, aluminum alloy and magnesium alloy called light alloy.
Many countries know the importance of titanium materials and they are research, development and application of the titanium material.
Titanium in the 1950s is an important structural metal. It has high strength, good corrosion resistance, high heat resistance and easy welding characteristics, used in various fields, especially high strength, easy welding performance is conducive to the manufacture of golf club head.
In 1954, USA succeeded in developed Ti (titanium)-6Al (aluminum)-4V (alum) alloys.
Ti-6Al-4V alloy have heat resistance, strength, ductility, toughness, formability, weldability, corrosion resistance and biocompatibility aspects to achieve better standards. The people use of Ti-6Al-4V alloy arrived for 75 to 85% of all titanium alloys.
When the hardness of titanium is greater than the HB350, the cutting will be particularly difficult. When the hardness of the titanium alloy is less than the HB300 is prone to stick the knife phenomenon is not easy to cut.
Titanium alloy, the chemical affinity of the tool material, cutting power under the conditions of the high cutting temperature and per unit area, the tool is very prone to adhesive wear, such as the <ex. Fig. 1>.
Titanium thermal conductivity is very small (equivalent to S45C 1/5 ~ 1/7),
The chip and rake face contact length is very short, the heat is not easy to release when the cutting. The heat is mainly concentrated in the smaller scale of the cutting area and near the cutting edge. The cutting temperature is high.
Chemical activity of titanium in the high cutting temperature, the external can easily absorb the oxygen and nitrogen in the air. They changed their characteristic easily. (ex. Hard and brittle) At the same time of plastic deformation in the cutting process can also cause surface hardening.
Chilled phenomenon will not only reduce the fatigue strength of parts and easy damage tool. So it is a very important feature when cutting titanium.
Titanium Alloy blank pass through many process. It changes into hard, brittle and uneven in surface. The flutes damage caused this condition. ( We recommend Titanium series of WWB. WWB can easy to solute this difficult problem.) (ex. Fig. 4)
.jpg)
<Fig. 4>Titanium Alloy blank
The collection of points as above, please note the following important points when you produce Titanium and Titanium Alloy.
A. Select the appropriate tool.
B. Use high-pressure emulsion machining (ex. Fig. 5)
C. Correct cutting data.
D. Programs (CAM) is also very important.
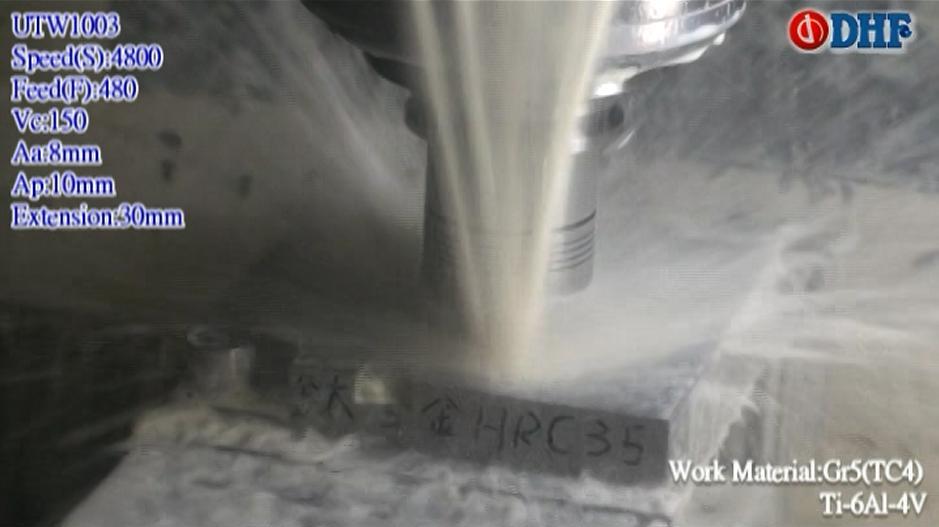
<Fig. 5> Example for use high-pressure emulsion machining
Understand the product feature and the right choice in order to show the excellent tooling capacity.
Written by DHF Technology Center